The Kovové lití pod tlakem proces může produkovat složité tvarované výrobky a může nabídnout vynikající rozměrovou přesnost a povrchovou úpravu. Je to také vysoce efektivní výrobní proces a může konkurovat jiným výrobním metodám. Stroj na tlakové lití má pevnou nebo krytovou polovinu a vyhazovací polovinu, která obsahuje vtokový otvor, vtoku a systém žlabů. Roztavený kov se vstřikuje do forem, kde se ochladí a ztuhne, aby se stal hotovým výrobkem. Tlakové lití nabízí řadu výhod, které z něj činí atraktivní možnost výroby. Má nižší náklady na nástroje než jiné výrobní procesy a umožňuje vyrábět díly s úzkými tolerancemi. Eliminuje také potřebu dalšího obrábění a umožňuje vytvářet tenké stěny. Pro zajištění přesnosti používají výrobci k řízení procesu řadu nástrojů. Patří mezi ně vyhazovač, běžce, sušenka (nebo sprue) a blesk. Tyto prvky jsou umístěny uvnitř dutiny formy a používají se k nasměrování roztaveného kovu do a ven z formy.
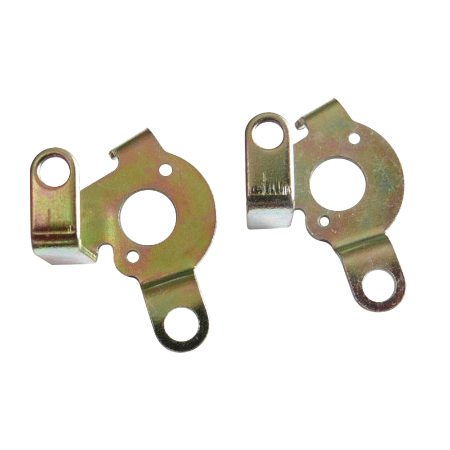
Na rozdíl od vstřikování plastů vyrábí tlakové lití součásti, které jsou pevnější a lehčí. Jsou rozměrově stabilní a bez větších obtíží zvládají i úzké tolerance. Tento proces také nabízí lepší povrchovou úpravu než jiné výrobní metody. Výrobci často podrobují výsledné produkty pískování a dalšímu zpracování pro bezvadný povrch. Poté jsou připraveny k odeslání nebo použití. Tyto výhody z něj dělají oblíbenou volbu pro mnoho různých průmyslových odvětví. Tlakovým litím lze vyrábět složité tvarované výrobky z lehkých kovů s vysokou přesností. Je zvláště užitečný pro díly, které musí odolávat vysokým teplotám a tlakům, jako jsou součásti automobilového a lékařského vybavení. Může také poskytnout vynikající povrchovou úpravu, srovnatelně sníženou poréznost a rozměrovou přesnost. Proces zahrnuje čtyři hlavní kroky: přípravu matric, vstřikování, chlazení a vyhazování. Formy jsou postříkány lubrikantem, aby se zabránilo přilepení roztaveného kovu. Poté je roztavený kov vstřikován do forem pod vysokým tlakem. To zajišťuje, že roztavený kov je vtlačen i do těch nejmenších rohů formy a zmírňuje smršťování.
Kov se pak ochladí ve formě, dokud neztuhne. Poté se poloviny formy oddělí a vyhazovací čepy vytlačí odlitek z formy. Jakýkoli přebytečný kov je pak oříznut pomocí různých nástrojů. Kvalita tlakově litého dílu závisí na jeho konstrukci a kovové slitině. Tlakové lití je flexibilní proces, který lze použít pro různé aplikace. Umožňuje vysokou rychlost výroby a vytváří jednotnou kvalitu, která vyžaduje méně práce než jiné způsoby výroby kovových dílů. Tato flexibilita z něj dělá oblíbenou volbu pro automobilový, letecký a lékařský průmysl. Kovové slitiny používané při tlakovém lití lze upravit tak, aby vyhovovaly specifickým potřebám. Například zinek se často používá v tlakově litých dílech, aby se zajistilo, že kov má nízkou teplotu tání. Poskytuje také dobrou odolnost proti korozi a hladký povrch.
Kovová raznice je rozdělena na dvě části – pevnou neboli krycí polovinu a vyhazovací polovinu. Polovina ejektoru je vybavena vtokovým otvorem, žlábkem a vtokem pro směrování roztaveného kovu do dutiny formy. K vytlačení tlakového odlitku z formy se pak použije tažná tyč nebo vyhazovací kolíky. Je důležité vyhnout se podříznutí v návrhu vašeho dílu. Mohou způsobit smrštění tekutého kovu během tuhnutí, což může ovlivnit rozměry a vstřikovací tlak součásti. Tlakové lití může být nákladově efektivní způsob výroby součásti. Důvodem je to, že jeden díl může nahradit více komponent, čímž odpadá sekundární frézování, vyvrtávání, vystružování a broušení. Kromě toho je proces neuvěřitelně přesný a má velmi nízkou zmetkovitost. Počáteční investice do kovových forem však může být vysoká. Celkové náklady na tlakové lití lze snížit výběrem menší formy s více dutinami.
Během procesu odlévání je roztavený kov vstřikován do forem pod vysokým tlakem. Tento tlak se udržuje, dokud roztavený kov neztuhne v dutině formy. Čas, který to zabere, závisí na geometrické složitosti formy a požadované tloušťce stěny hotového výrobku. Oříznuté odlitky jsou pak vyhazovány z forem vyhazovacím systémem. Vyhazovací systém se skládá ze dvou částí: vyhazovacích kolíků a vyhazovací desky. Je důležité zvolit správný vyhazovací systém pro váš projekt, protože to ovlivní výslednou kvalitu odlitků. Pokud jsou vyhazovací kolíky příliš slabé, nepodaří se jim vytlačit odlévané díly z matric, což má za následek vadný odlitek.